
20XT 4WD Drivetrain
As lead drivetrain engineer for the JHU Baja SAE team, I oversee the design, testing, and manufacturing of all power transmission components of our 2024 vehicle's 4WD system.
Project Overview
My primary goal as a subsystem lead was to facilitate the design of more lightweight and aggressive components to maximize peak performance while mitigating risk. This was achieved through the implementation of rigorous design reviews and a formal "design freeze" process to ensure all components were manufacturable, and analysis was set up and conducted properly. I placed additional emphasis on allowing each component to be serviced independently with minimal dependencies to reduce the impact of failure.
​
Check out some design highlights below!

Drivetrain assembly in context to frame assembly
Design Highlights

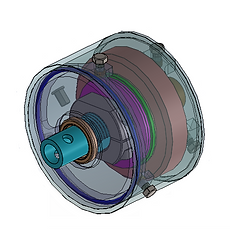

20XT Front Differential
20XT Torque Limiter
20XT 2WD/4WD Shifter
The third iteration of our overrunning differential features sprag clutches pressed into aluminum cups in order to eliminate the differential cage and decrease the size of the bevel gears.
​
The aluminum cups were used to mount inboard brake rotors and reduce unsprung weight, therefore improving suspension packaging.
​
This year's front differential saw a 17% weight reduction, due in part to improved load-data processing and case optimization using Ansys.
This friction-slip clutch was designed to replace its bulky off-the-shelf equivalent. As a smaller and lighter custom solution, it reduces peak loads seen by the propshaft and front drivetrain, allowing components to be designed to lower driving conditions, ignoring inertial spikes seen during jump landings and such.
​
The torque limiter is tuned using a large locknut and Belleville spring washers, which control the pressure between two plates of sintered copper friction materials.
This second iteration of the shifter allows the driver to switch between 2WD and 4WD and control its handling characteristics, acceleration performance, and utilize 4WD to clear obstacles.
​
It features a pair of dog clutches that engage and disengage quickly by use of a linear actuator, allowing the driver to focus on driving the vehicle.
​
Its robust design allowed us to integrate it into our transfer case, and shrink the drivetrain's overall packaging.
Drawing Tree
This spreadsheet was used to track each component of the car, from its modeling through its final manufacturing and assembly. At a glance, subteam leads can update the status of models as they are completed, frozen, or released for manufacturing.

20XT Drawing Tree
Master Design Sheet
This spreadsheet was used to set design factors for various design factors of components based on test results, failure risk, and impact of failure. It also compiles all material properties and expected system loads to ensure each component designer operates with the same allowable and loads for their analysis.
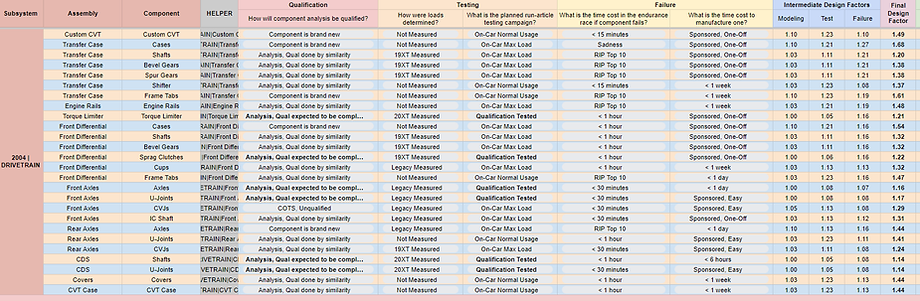
20XT Master Design Sheet
Design Freeze Checklist
This checklist was used to ensure each aspect of a component, including analysis, integration, manufacturability, logistics, and serviceability were checked and finalized before freezing a part to be greenlighted for procurement and/or manufacturing.
​
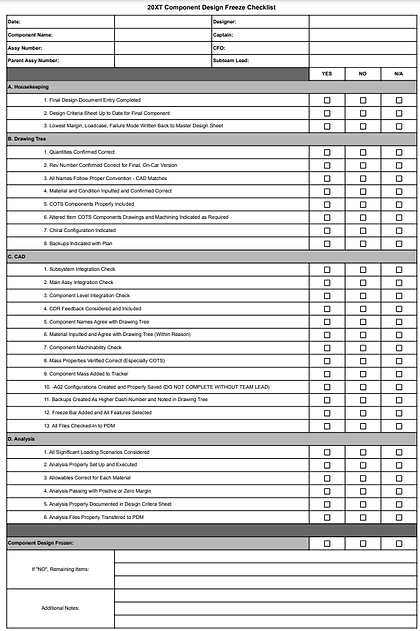
20XT Component Freeze Checklist
Manufacturing
With the recent addition of CNC capabilities being made available to our workspace, we relied heavily on the CNC to make most of our parts in-house. Check out some photos of the drivetrain assembly being manufactured below!

Layout of all CNC compoennts featured on the 20XT drivetrain assembly

Front drivetrain frame jigging

Aluminum-welded CVT case
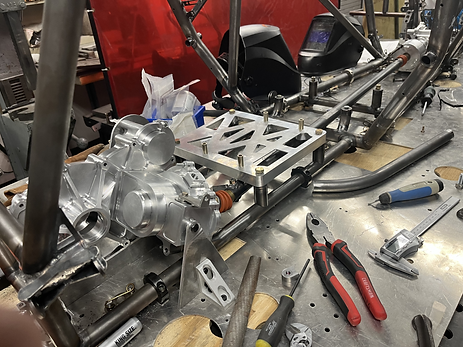
Rear drivetrain frame jigging

"Bevel dawg" profiling

Blue Jay Racing!